Half way through 1977 I was asked if I wanted to go to Dampier
in Western Australia (WA) - actually I was told I was going, the question
was rhetorical. Hammersley Iron (HI), with whom Automation Industries
(AI) had a contract, needed help with a problem.
The rails in their track were quite literally wearing out under the high
loads of the ore trains. They decided that the way to combat this attrition
rate was to get get stronger rails. To this end they purchased a consignment
of rails made from high tensile strength alloy steel. The rails would
be welded into continious lengths by a Westrail welding crew onsite at
Dampier. AI would provide an "expert", yours truely, to ultrasonically
hand test all the welds.
|
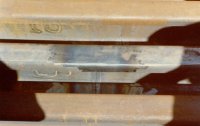 |
This is a weld that cracked as I was testing it. The high
alloy content of the steel meant that defects in the welds were common.
In conjunction with the "springiness" of the steel |
SRS140 at "Five Mile" the main service depot for Hammersley Iron's rail fleet |
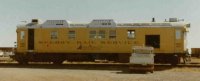 |
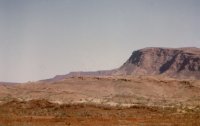 |
Some of the local scenery |
SRS140 passing the site of a recent derailment. In most cases the wagons are just pushed aside by a bulldozer and the track relaid. Bogies and wheels are recovered but the wagons themselves will be cut up for scrap. |
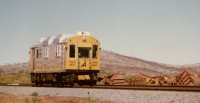 |
|
|